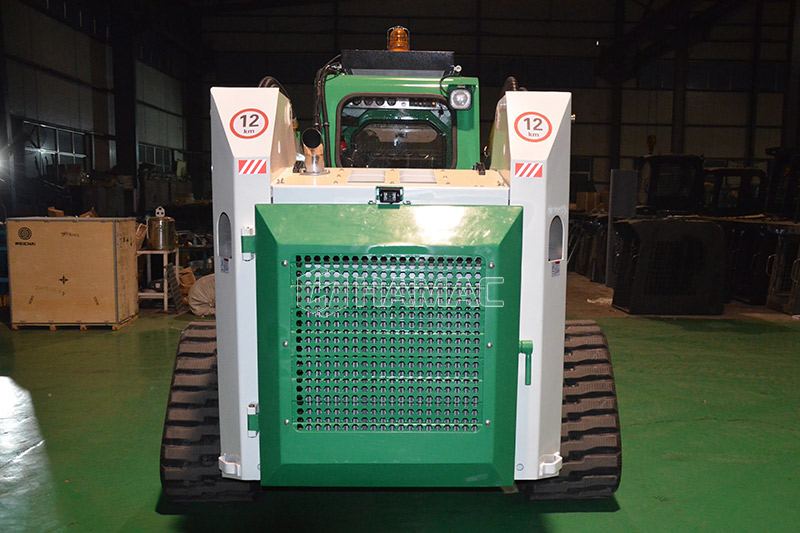
Earth-moving Machines
Only a loader with the right bucket can increase productivity
Source: Hamac Machinery
When you choose a wheel loader, there are many options to weigh - size, power, technology, comfort and safety features - but perhaps the most important is the bucket. Choosing the wrong bucket can negatively impact your bottom line by reducing productivity, increasing fuel consumption and causing premature wear and tear. In fact, one wrong choice can increase your costs by 10 to 20 percent. So, how do you make the right choice? Here are three factors to consider when choosing a bucket (and loader)
1. The type of material to be handled
The density of the material plays the biggest role in bucket selection, in addition to moisture content, hardness and wear level. Choose based on the heaviest material you intend to handle most of the time. The names of the buckets - general purpose, heavy duty, abrasion resistant - usually reveal the type of material they will be handling. Keep in mind that you probably won't be able to fill a large bucket with very heavy, hard-to-pass material. A smaller bucket may be more advantageous than a larger bucket because it will allow your loader to cycle faster.
2. Bucket size
Don't fall into the myth that a bigger bucket means more production. Choosing a bucket that pushes your loader beyond the recommended capacity limit - even by just a few percentage points - will accelerate wear, reduce component life and risk unexpected breakdowns. Any short-term gains you realize are likely to be wiped out by repairs and downtime. Instead, follow this simple three-step process.
Consider the capacity of the truck you are loading.
Determine how much cargo you need to move each day.
Choose the bucket size that will give you the ideal pass match.
In many cases, first determine the size of your bucket, then choose a wheel loader that can accommodate it, not the other way around.
3. Bucket design
Choosing the cheapest bucket is not always the best strategy. Two buckets may look the same, but differ greatly in design, making the less expensive option the more costly one. The following are some design features to consider.
Harder, thicker plate material for longer bucket life
High-quality edges, side blades and teeth that are worthwhile in terms of productivity, reusability and ease of installation
Longer bucket base plate for reduced cycle time
Curved side plates and integrated splash guards for improved material retention
Wear protectors and extra guards to reduce damage and extend bucket life
Quick coupling for increased productivity if you change buckets frequently
Add-ons such as bolt-on teeth and cutting edges make a bucket even more versatile
1. The type of material to be handled
The density of the material plays the biggest role in bucket selection, in addition to moisture content, hardness and wear level. Choose based on the heaviest material you intend to handle most of the time. The names of the buckets - general purpose, heavy duty, abrasion resistant - usually reveal the type of material they will be handling. Keep in mind that you probably won't be able to fill a large bucket with very heavy, hard-to-pass material. A smaller bucket may be more advantageous than a larger bucket because it will allow your loader to cycle faster.
2. Bucket size
Don't fall into the myth that a bigger bucket means more production. Choosing a bucket that pushes your loader beyond the recommended capacity limit - even by just a few percentage points - will accelerate wear, reduce component life and risk unexpected breakdowns. Any short-term gains you realize are likely to be wiped out by repairs and downtime. Instead, follow this simple three-step process.
Consider the capacity of the truck you are loading.
Determine how much cargo you need to move each day.
Choose the bucket size that will give you the ideal pass match.
In many cases, first determine the size of your bucket, then choose a wheel loader that can accommodate it, not the other way around.
3. Bucket design
Choosing the cheapest bucket is not always the best strategy. Two buckets may look the same, but differ greatly in design, making the less expensive option the more costly one. The following are some design features to consider.
Harder, thicker plate material for longer bucket life
High-quality edges, side blades and teeth that are worthwhile in terms of productivity, reusability and ease of installation
Longer bucket base plate for reduced cycle time
Curved side plates and integrated splash guards for improved material retention
Wear protectors and extra guards to reduce damage and extend bucket life
Quick coupling for increased productivity if you change buckets frequently
Add-ons such as bolt-on teeth and cutting edges make a bucket even more versatile
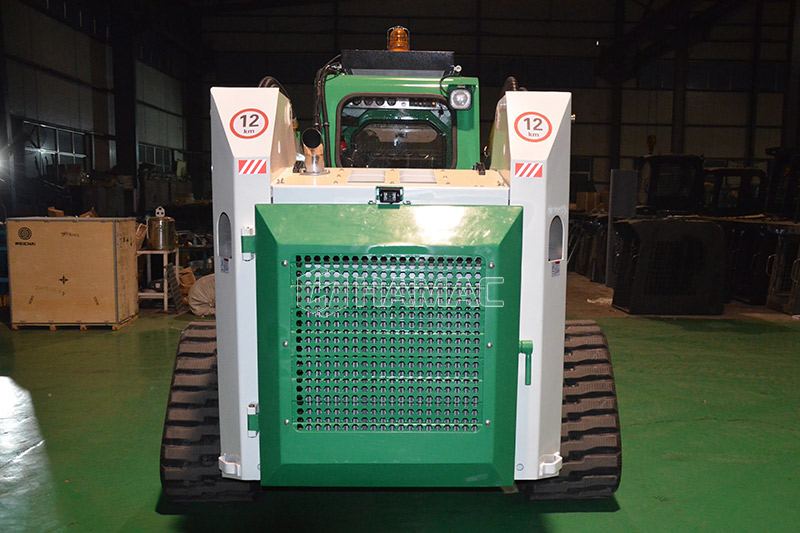
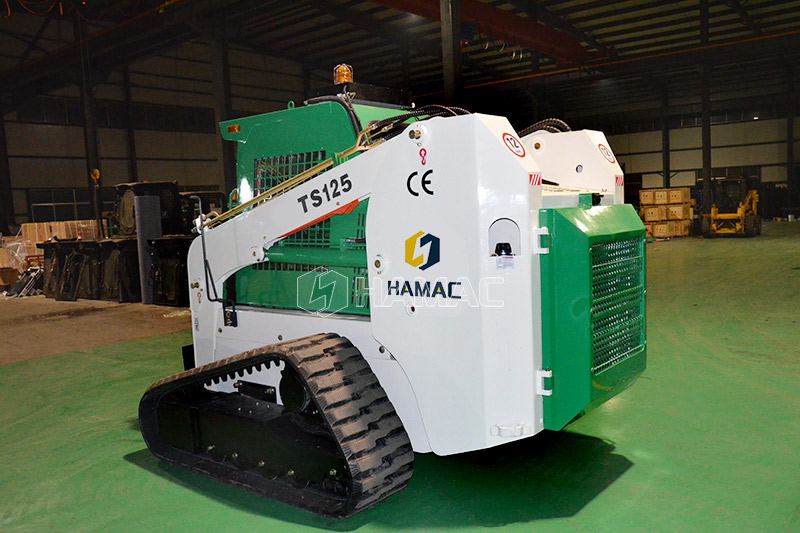
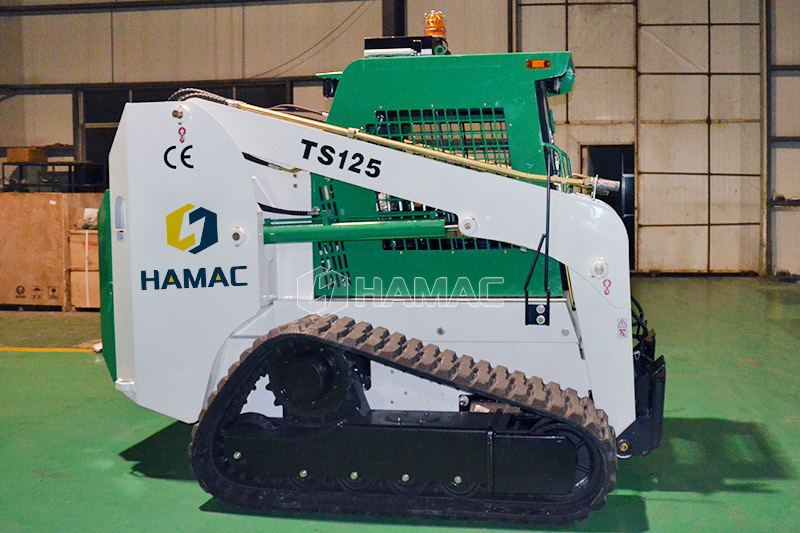
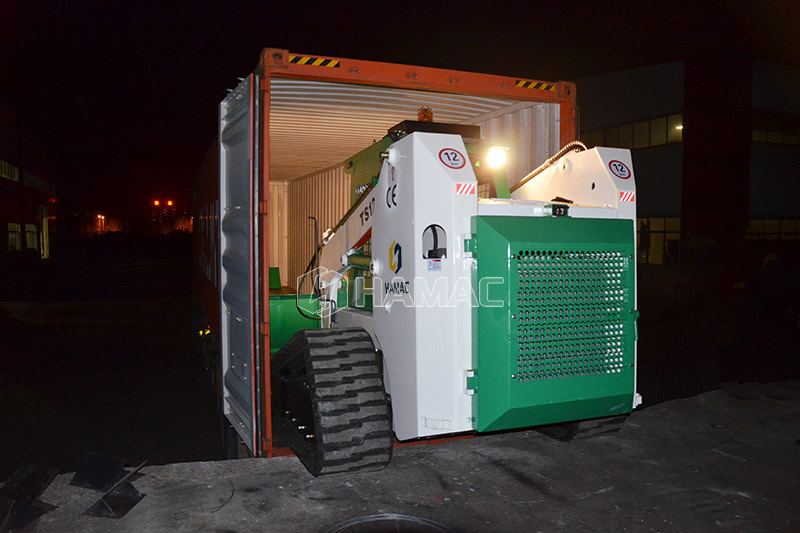
There is no lowest price, only lower price. You get what you pay for. We hope you are looking for the perfect working performance of the equipment, not the low-priced inferior goods. HAMAC only provide our clients with high quality machines. Wish a cooperation with you in the future.
Tags :
skid-steer loadermini skid steer loaders for saleskid steer tracksskid steer loader supplier
3YK2160 vibrating screen and belt conveyorsmobile concrete batching plantconcrete block making plantbobcat s130 for salesmall concrete pump machine in Bissau
concrete mixers for sale in south africaconcrete trailer pump for saleschwing concrete pump trucks for saleconcrete pump for saleputzmeister concrete pump for sale